What is mica?
Mica is a kind of hydrated aluminosilicate with complex structure. It is often composed of granite with quartz and feldspar, or symbiotic in other ores. The main ore-forming ones are pegmatites.
Mica is a general term for the mica group of minerals, which are aluminosilicates of metals such as potassium, aluminum, magnesium, iron, and lithium.
Mica ore mainly includes biotite, phlogopite, muscovite, lepidolite, sericite, green mica, lepidolite, etc. Aventurine is a mixed mineral of mica and quartz. The most widely used in industry are muscovite and phlogopite, and lepidolite is an important mineral raw material for lithium extraction.
What are the properties of mica?
The characteristics of mica are insulation, high temperature resistance, luster, stable physical and chemical properties, good heat insulation, elasticity and toughness. After being processed into mica powder, it has better sliding property and stronger adhesion.
What are the uses of mica?
1. Biotite industry mainly uses its insulation and heat resistance, as well as acid resistance, alkali resistance, compression resistance and peeling resistance, as an insulating material for electrical equipment and electrical equipment; secondly, it is used in the manufacture of steam boilers, Furnace windows and mechanical parts of smelting furnaces.
2. Mica crushed and mica powder can be processed into mica paper, and can also replace mica sheet to manufacture various insulating materials with low cost and uniform thickness.
3. The main purpose The most used in industry is muscovite, followed by phlogopite. It is widely used in building materials industry, fire protection industry, fire extinguishing agent, welding rod, plastic, electrical insulation, papermaking, asphalt paper, rubber, pearlescent pigments and other chemical industries.
4. Ultrafine mica powder can be used as functional filler for plastics, coatings, paints, rubber, etc., which can improve its mechanical strength, enhance toughness, adhesion, aging resistance and corrosion resistance.
5. In addition to its extremely high electrical insulation, acid and alkali corrosion resistance, elasticity, toughness and sliding properties, heat and sound insulation, and small thermal expansion coefficient, it is also the first to introduce smooth surface, large diameter-to-thickness ratio, and regular shape. , strong adhesion and so on.
How to process mica powder?
1. Mica beneficiation and purification
The beneficiation and purification methods of mica are divided according to the properties and types of mica. Generally speaking, flake mica generally adopts manual sorting, friction beneficiation, shape beneficiation, etc., while crushed mica adopts wind separation and flotation.
The beneficiation and purification method of flake mica
1. Manual pickingOn the mining face or the ore pile at the pit, the mica that has been separated from the monomer is selected; the conjoined body of mica and gangue is broken with a hand hammer, and then the mica is selected.
2. Friction beneficiationAccording to the difference between the sliding friction coefficient of sheet mica and the rolling friction coefficient of round gangue, mica and gangue are separated. One of the equipment used is the inclined plate sorter.
The machine is composed of a set of metal inclined plates. During the selection process, the large gangue rolls down to the waste rock pile; the mica and smaller gangue blocks are blocked by the weir plate and fall to the next inclined plate through the gap. Repeat the above process on the inclined plate in turn, so that the mica and the gangue are gradually separated.
3. Shape dressingAccording to the different shapes of mica crystals and gangue, the ability to pass through the sieve gap or sieve hole during sieving is different, so that mica and gangue are separated. When sorting, a sieve with more than two layers of different screen surface structures is used. Generally, the first layer of screen mesh is square. When the raw ore enters the screen surface, due to vibration or rolling, the flake mica and small pieces of gangue can be removed from the screen. The slit of the strip screen leaks to the screen surface of the second layer. Because the second layer is a grid screen, the gangue can be screened out and the flaky mica is left.
The beneficiation and purification method of chip mica
1. Mica flotationThe ore is crushed and ground to dissociate the mica and the gangue monomer, and under the action of the flotation agent, the mica becomes a foam product and is separated from the gangue.
There are currently two flotation processes: one is to flotate mica with amine collectors in an acidic medium, the pH value is controlled below 3.5, desliming is required before flotation, and the solid content of the pulp is 30% to 45%;
The second is to use anionic collectors for flotation in an alkaline medium, the pH value is controlled at 8 to 10.5, and desliming is also required before selection. The mica flotation process needs to be selected many times.
2. Mica selectionMica wind selection is mostly realized through special equipment. The technical process is generally: crushing → screening and classification → air selection.
After the ore is crushed, mica basically forms flakes, while the gangue minerals feldspar and quartz are block-like particles. According to this, the selected materials are pre-divided into narrower grades by multi-level grading, and the special air separation equipment is used for sorting according to the difference of their suspension speed in the airflow.
2. Mica peeling
The raw mica is peeled into mica flakes of various specifications, which is called mica flakes. At present, there are three kinds of peeling methods: manual peeling, mechanical peeling and physical and chemical peeling, which are mainly used for processing various flake mica, such as thick flake mica, thin mica, electron tube mica, etc. Most of them are manual operations.
3. Mica powder fine grinding and ultra-fine grinding
Dry grinding mica powder processing method and technical index
The fine grinding and ultra-fine grinding of mica, that is, the production of mica powder, has two types:
dry method and
wet method.
The dry fine grinding and ultrafine grinding equipment of mica mainly include
ball mill,
coarse powder grinding mill,
Raymond mill,
high pressure grinding mill,
HGM ultrafine grinding mill, etc.
In the production of ultra-fine mica powder, dry classification equipment (turbine air centrifugal classifier) is generally required; in the production of coarse mica powder, a plane shaking screen, a suspension screen, a vibrating screen, etc. are generally used for classification.
Quality index requirements for dry-milled mica powder
Specification |
Screen remaining /% |
Sand content /% ≤ |
Loss on ignition /% ≤ |
Loose density /(g/cm³) ≤ |
Water content /% ≤ |
Whiteness /% ≥ |
38μm |
75μm,≤0.1 38μm,≤10 |
0. 5 |
5 |
0.25 |
1 |
70 |
45μm |
112μm,≤0.1 45μm,≤10 |
5 |
1 |
70 |
75μm |
150μm,≤0.1 75μm,≤10 |
0.6 |
5 |
0.28 |
1 |
65 |
90μm |
180μm,≤0.1 90μm,≤10 |
1.0 |
5 |
0.28 |
1 |
65 |
125μm |
250μm,≤0.1 125μm.≤10 |
5.0 |
0.3 |
1.0 |
65 |
Technical indicators of dry ground mica powder
Processing method and technical index of wet grinding mica powder
The main equipments for wet grinding mica powder are wheel mill, sand mill, stirring mill, high pressure homogenizer, etc. Wet-milled mica powder has the advantages of pure texture, smooth surface, large diameter-to-thickness ratio, and strong adhesion.
Therefore, wet-milled mica powder has better performance, wider application and higher economic value. In particular, the mica powder as the base material of pearlescent mica generally requires wet grinding of the mica powder. Wet grinding technology is the main development trend in the production of fine mica powder.
Wet-milled mica powder quality index requirements
Specification |
Particle size distribution |
Magnet suction /X10-g ≤ |
Sand content /% ≤ |
Loose density /(g/cm³) ≤ |
Water content /% ≤ |
Whiteness /% ≥ |
900μm |
μm |
+900 |
+ 450 |
+300 |
-300 |
400 |
1.0 |
0.36 |
1.0 |
45 |
% |
<2 |
65士5 |
<10 |
— |
450μm |
μm |
+450 |
+ 300 |
+150 |
-150 |
% |
<2 |
45士5 |
— |
<10 |
300μm |
μm |
+ 300 |
+ 150 |
+75 |
-75 |
800 |
1.5 |
50 |
% |
<2 |
50士5 |
— |
<10 |
150μm |
μm |
+150 |
+75 |
+45 |
-45 |
% |
<2 |
40士5 |
— |
<30 |
75μm |
μm |
+75 |
— |
400 |
1.0 |
0.34 |
% |
<2 |
45μm |
μm |
+45 |
— |
% |
<2 |
What are the commonly used mica powder grinding mills?
Mica powder grinding mill machines are the pulverizers that grind mica rock into 30-3000 mesh mica powder.
According to the fineness of the processed mica powder, there are mainly the following categories:
- 1.European Version Coarse Grinding Mill: 0-3 mm
- 2.Raymond Mill: 35-400mesh fine powder making
- 3.HGM Ultrafine Grinding Mill: 150-2500 mesh ultrafine powder making
1. European Version Coarse Grinding Mill: coarse powder making

European version coarse powder mill
Maxing Feeding Size: 80 mm
Ouput Size: 0-3 mm
Capacity: 8-100 t/h
Advantages: European Version Coarse Grinding MIll is generally used after jaw crusher, impact crusher or hydraulic cone crusher.
Because the feeding particle size of European version coarse grinding is between 30-50mm, and the discharging particle size is adjustable in the range of 0-3mm, 0-5mm and 0-8mm.
The production capacity can reach up to 100 tons per hour. Uniform discharge and considerable output.
2. Raymond Mill: fine powder making
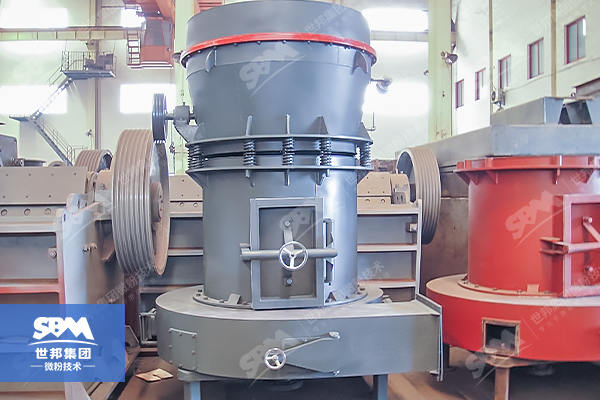
YGM High Pressure Raymond Roller Grinding Mill
Maxing Feeding Size: 40 mm
Ouput Size: 613-33 micron (35-400mesh)
Capacity: 1-25 t/h
Applicable materials: Pumice, Calcium carbonate, limestone, kaolin, limestone, calcite, marble, talcum, barite, gypsum, dolomite, bentonite mud, mica
Advantages: Raymond mill is a cost-effective fine powder processing equipment. Easy to operate and efficient.
3. HGM Ultrafine Grinding Mill: ultrafine powder making

HGM Ultrafine Powder Grinding Mill
Maxing Feeding Size: 20 mm
Ouput Size: 74-5 micron (150-2500 mesh)
Capacity: 0.5-45 t/h
Applicable materials: Pumice, Calcium carbonate, limestone, kaolin, limestone, calcite, marble, talcum, barite, gypsum, dolomite, bentonite mud, mica, etc.
Advantages: HGM ultra-fine grinding is very different from Raymond grinding in structure. It adopts a multi-ring, layered grinding structure. Due to its multi-ring, multi-roller structure, it is possible to process finer powders and at the same time be more efficient.
WHO WE ARE?
SBM Ultrafine Powder Technology Co., Ltd. is one of the premier manufacturers for equipment in the mining, grinding, coating,packing, recycling and process industries.
With SBM Ultrafine Powder Technology unique knowledge and innovative solutions, SBM helps many customers improve their operational efficiency, reduce risks and increase profitability.
SBM Ultrafine Powder Technology products can be divided into
crushing equipment, grinding equipment, drying equipment, screening equipment, conveying equipment and
auxiliary equipment.
SBM Ultrafine Powder Technology products have passed the quality system certification of ISO9001:2008, and the European CE certificate.
SBM sincerely welcome local distributors join us together to shape SBM Ultrafine Powder Technology brand and delivery high value-added equipment products in the global market around world.
SBM Ultrafine Powder Technology is an international high-tech enterprise which integrates the research and development, production and sales.
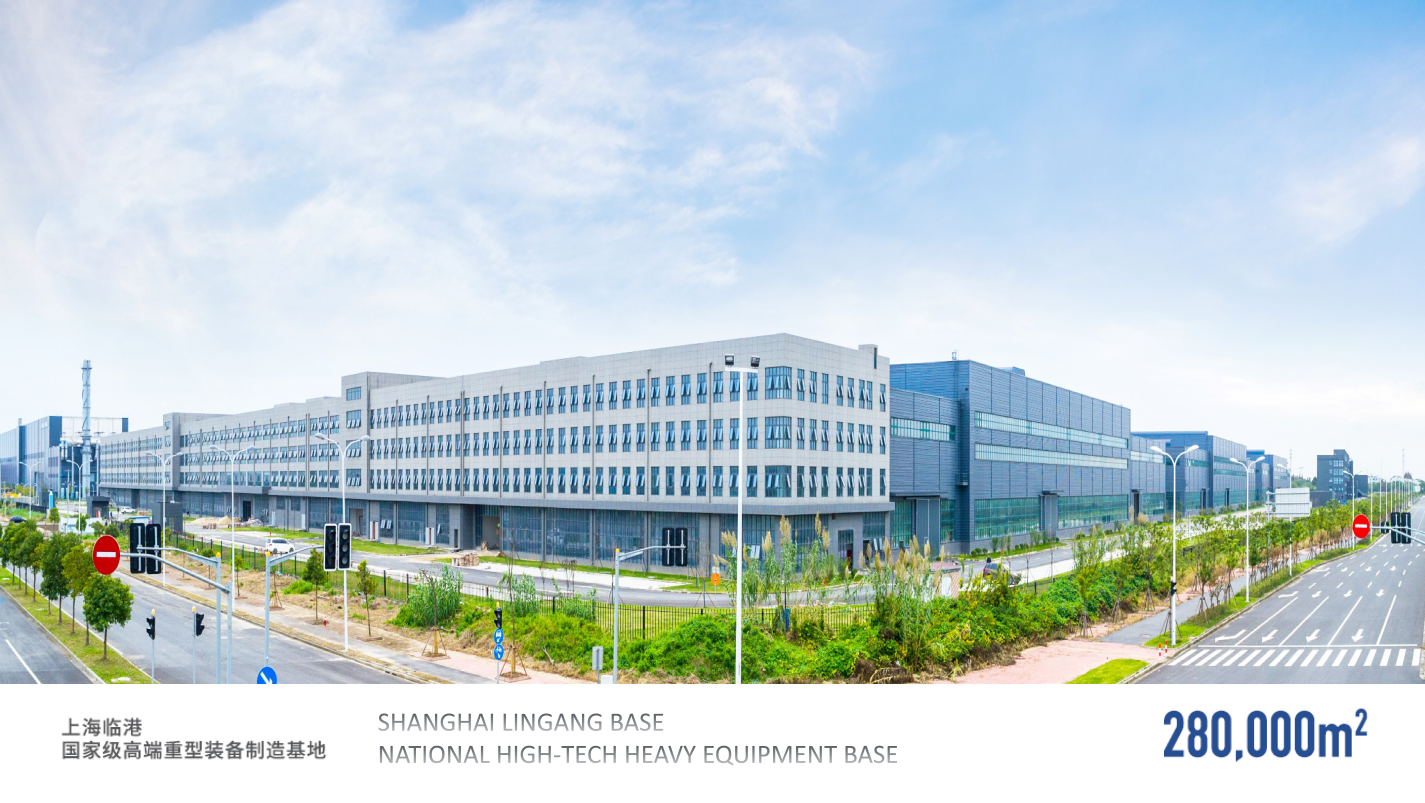
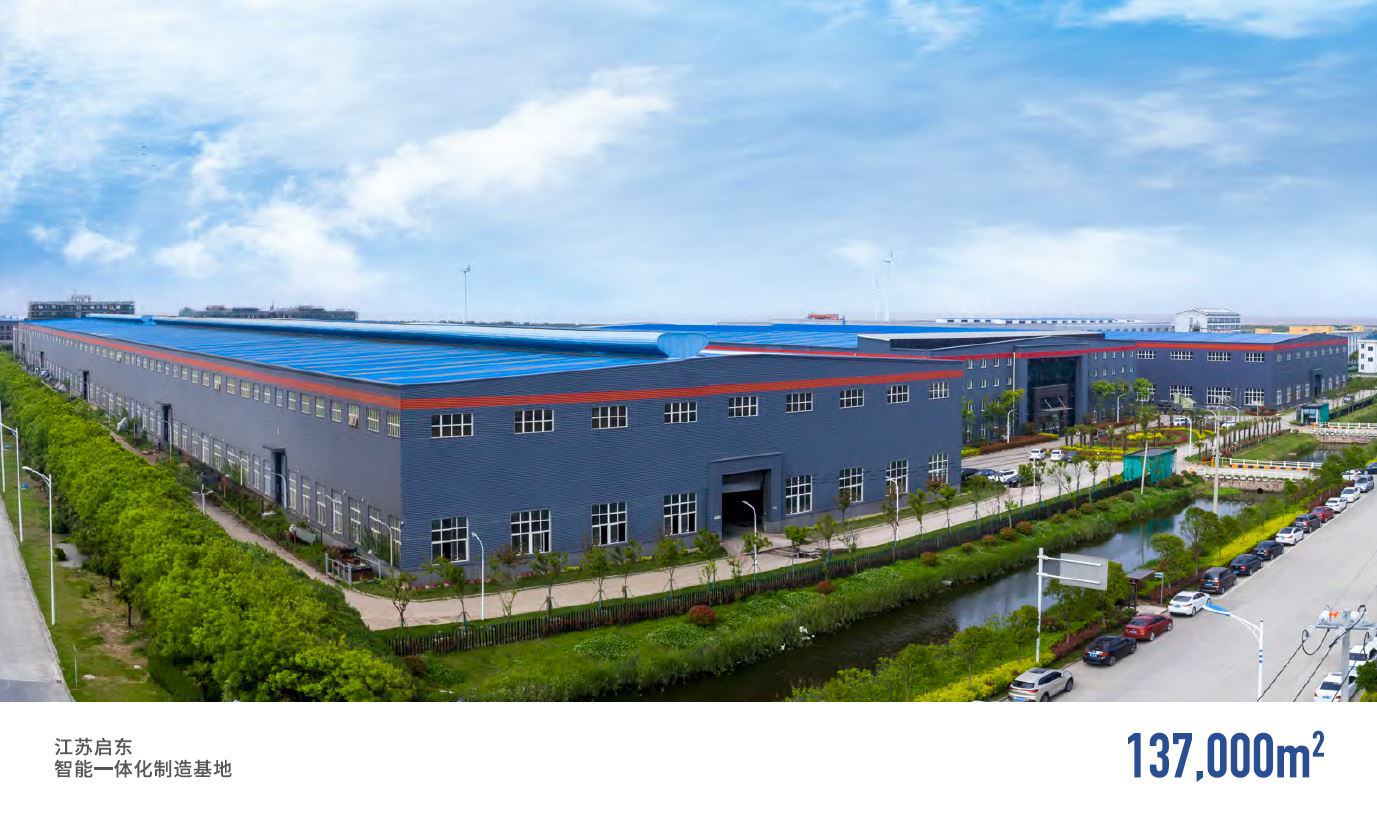
HOW TO BUY?
- 1. Engineering project design
- 2. Equipment purchasing and manufacturing
- 3. Engineering project construction
- 4. Installation and Commissioning service
- 5. After-sales service
WHICH MODELS CAN BE SELECTED FOR PROCESSING ULTRA-FINE POWDER?
HGM grinding mill: 74-5 micron(200-2500 mesh); D97=5 micron
YGM Raymond mill: 613-33 micron(30-325 mesh); D90=30 micron
CLUM vertical roller mill: 20-5 micron(600-3000 mesh); D50=2 micron D97=4 micron
HOW TO GET THE LATEST QUOTATION?
You can leave a message online or contact
SBM Ultrafine Powder Technology directly:
WhatsApp: +8613512155195